FRACAS — СИСТЕМА ОТЧЕТНОСТИ ОБ ОТКАЗАХ, АНАЛИЗЕ ОТКАЗОВ И КОРРЕКТИРУЮЩИХ ДЕЙСТВИЯХ
Устранение отказов — это просто
В этом уроке мы познакомим вас со статьей Рики Смита, эксперта в области лучших практик технического обслуживания и надежности.***
Насколько хорошо в вашей организации выполняется идентификация отказов оборудования?
Конечно, вы замечаете отказы, когда они происходят, но сможете ли вы определить, когда повторяющиеся отказы начнут создавать серьезные проблемы с надежностью оборудования?
Большинство компаний начинают свой путь в работе над повышением надежности с выполнения поиска коренных причин (RCA) применительно к отказам, влекущим наиболее дорогостоящие последствия. Тем не менее, целесообразно сконцентрировать свои усилия на раннем обнаружении отказов и уменьшении их числа до приемлемого уровня.
FRACAS (Failure Reporting, Analysis, and Corrective Action System (FRACAS) — система отчетности об отказах, анализе отказов и корректирующих действиях.
FRACAS — это отличный инструмент, который можно использовать для предотвращения и устранения отказов. Это процесс, который позволит идентифицировать любые отчеты из вашей CMMS* / EAM**.
Эти отчеты могут включать:
- отклонение от запланированной стоимости выполнения работ;
- среднее время между отказами;
- среднее время ремонтов;
- доминирующие паттерны отказов вашего оборудования;
- общие связи сигналов, возникающих между отказами, например, такие как «недостаток смазки» (возможно потому, что лубрикатор не соответствует стандартам или специфике требований условий вашей эксплуатации) и т.п.
***
Прежде чем читать дальше — честно ответьте на следующие вопросы, чтобы увидеть, есть ли у вас проблемы с идентификацией отказов, их устранением или смягчением последствий, а также уменьшением их влияния на общий процесс производства и надежность других активов:
- Можете ли вы определить 10 единиц оборудования, которые имели наибольшие потери вследствие функциональных отказов, на основании отчета о техническом обслуживании, выполненного при помощи информационной системы управления ТОиР?
- Можете ли вы определить суммарные потери, связанные с оборудованием в вашей организации и разнести их внутри процессов и оборудования за последние 365 дней?
- Можете ли вы идентифицировать компоненты, паттерны отказов которых соответствуют модели распределения отказов, представленной на Рисунке 1?
Рисунок 1
Во многих случаях, общая стоимость потерь от снижения требуемой надежности остается неизвестной, потому что причин ненадежности очень много. Проектирование, эксплуатация, обслуживание — каждая функциональная область вносит свой вклад в уменьшение надежности. Вот только несколько примеров возможных потерь:
1. Отказ оборудования (полный функциональный отказ)
- Отсутствие процедур профилактического технического обслуживания, смазывания, предупредительных замен узлов или комплектующих, эффективных восстановительных ремонтов.
- Невыполнение предписанных процедур по эффективному техническому обслуживанию.
2. Работа оборудования не достигает необходимых параметров (частичный функциональный отказ)
Возможные причины:
- Оператор не следует процедурам эффективной эксплуатации оборудования.
- Оператор не обучен обслуживанию оборудования.
- Руководство убеждено, что данная эффективность оборудования — это лучшее, чего можно достигнуть с учетом возраста и (или) состояния актива.
3. Выпуск некачественной продукции с первого раза (в связи с полным или частичным функциональным отказом)
Возможные причины:
- Руководство принимает концепцию — «отсутствие качества с первого раза — это не потеря, потому что продукт можно отправить на переработку».
4. Преждевременная поломка оборудования
Возможные причины:
- Неэффективные или вообще отсутствующие процедуры ввода в эксплуатацию после замены оборудования или его узлов.
***
Процесс проактивной модели технического обслуживания
Проактивная (или иначе, упреждающая) модель рабочего процесса — уничтожение ненадежности в процессе непрерывного улучшения технического обслуживания.
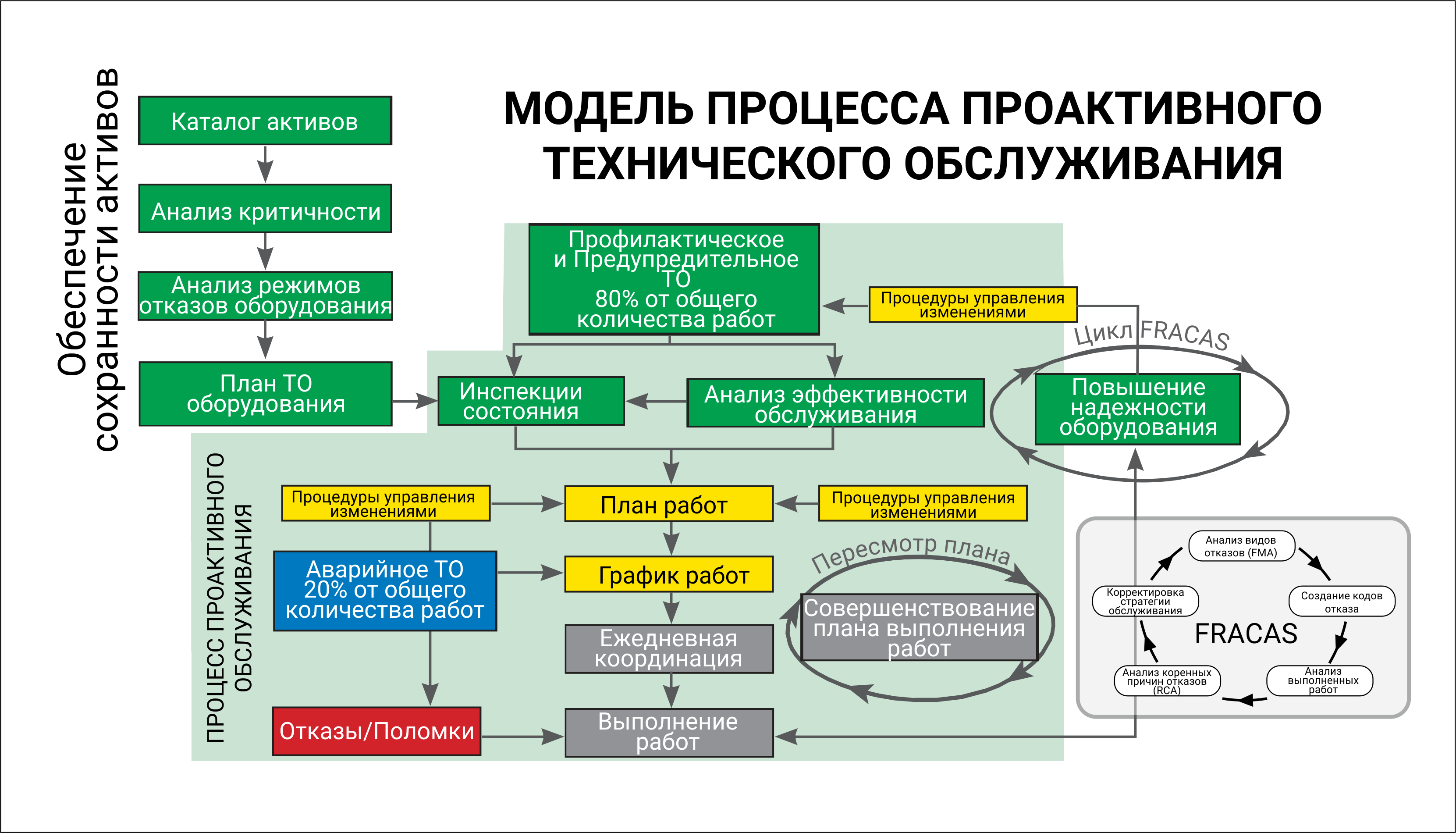
Рисунок 2
На Рисунке 2 изображена модель, показывающая шаги, которые необходимо сделать для перехода от реактивного к проактивному техническому обслуживанию. Если вы не знакомы с процедурами управления изменениями — можете получить информацию здесь — https://habr.com/ru/post/222863/
Внедрение модели проактивного технического обслуживания — ключ к устранению отказов оборудования. Встроенные в эту модель процессы непрерывного улучшения планов выполнения работ, анализ отказов и их причин, а также система корректирующих действий (FRACAS) помогут обеспечить надежность и ремонтопригодность, а также дать возможность улучшения этих показателей.
Элементы обеспечения сохранности активов (Рисунок 3), представленные в модели, являются основополагающими, так как они гарантируют, что все активы охвачены планом технического обслуживания. Такая 100% вовлеченность активов в единую систему управления является обязательным требованием для создания проактивного процесса технического обслуживания.
Вы не можете наладить постоянное улучшение, пока у вас не выстроены повторяющиеся процессы и отсутствует дисциплина их выполнения.
Цель модели проактивного технического обслуживания состоит в том, чтобы обеспечить дисциплину и повторяемость для ваших сервисных процессов.
FRACAS обеспечивает выполнение непрерывной работы по улучшению стратегии технического обслуживания.
Подумайте о FRACAS следующим образом:
Рисунок 4
Так как у вас возникают отказы оборудования, то вы используете определенные коды в CMMS / EAMS для записи выявленных причин каждого отказа.
Анализируя причины отказов на критических активах вы помогаете себе начать делать серьезные улучшения в надежности вашей работы.
Глядя на модель FRACAS (Рисунок 4), мы начинаем проводить анализ выполненных работ, чтобы решить, какую методику мы должны применить в каждом конкретном случае: анализ коренных причин отказов (RCA), RCM-анализ, или FMEA для снижения последствий и уменьшения числа отказов.
RCA позволяет нам корректировать стратегию прогнозирования и предотвращения отказов. Следует помнить, что даже самый тщательный анализ не раскрывает каждый вид отказа. Мониторинг производительности оборудования, выполняемый после того, как мы сделаем корректировку стратегии обслуживания, может выявить новые отказы, которые не охвачены этой стратегией. В этом случае вы должны создать новые коды для выявленных видов отказов, внести их в CMMS / EAM и далее отслеживать их при выполнении анализа выполненных работ. Таким образом, вы можете видеть, что это непрерывный цикл усовершенствования, который никогда не заканчивается.
***
Шаги по внедрению FRACAS
Основополагающими элементами эффективного FRACAS являются (см. Рисунок 3):
- валидация иерархии оборудования;
- анализ критичности;
- анализ режимов отказов оборудования;
- планы технического обслуживания.
FRACAS Чек-лист:
- Иерархия оборудования построена таким образом, чтобы подобные сбои на подобном оборудовании могли быть идентифицированы по всей организации.
- Анализ критичности разработан и утвержден таким образом, что критичность оборудования оценивается на основе пропускной способности производства, использованию активов, стоимости жизненного цикла, требований окружающей среды и безопасности.
- Анализ видов отказов с применением методик FMA, FMEA или RCM завершен для всех критических активов.
- Стратегия обслуживания разработана на все критическое оборудование таким образом, что техническое обслуживание позволяет предотвратить или предсказать отказы.
Шаг 1. Эффективная иерархия оборудования
Каталог активов (иерархия оборудования) должен быть разработан таким образом, чтобы была возможность предоставлять данные для управления программой проактивного обслуживания оборудования, включающей анализ отчетов об отказах или методику FRACAS (отчеты об отказах, система анализа причин отказов и корректирующих действий).
Для устранения отказов оборудования необходимо обеспечить успешное выполнение этого первого шага.
Рисунок 5
На Рисунке 5 отображены результаты одного завода, где зафиксировано 32 неисправности «деталь — подшипник» от электродвигателей разного размера («деталь» идентифицируется из выпадающего списка кодов CMMS / EAM на экране).
Один тип «Дефект — Износ» характерен для 85% отказов («Дефект» идентифицируется из выпадающего списка кодов CMMS / EAM на экране).
В 98% случаев «Причиной» оказалась «Ненадлежащее смазывание».
Используя эти данные можно выполнять анализ коренных причин отказов по общим взаимосвязанным отказам («Причина» идентифицируется из выпадающего списка кодов CMMS / EAM на экране).
Как только иерархия будет установлена, вы можете найти аналогичные сбои в однотипном оборудовании или по всему оборудованию в целом.
Иерархия оборудования должна соответствовать требованиям, установленным в стандарте организации. Должна быть заложена возможность анализа: «Деталь» -— «Дефект» — «Причина».
Обслуживающий персонал может не иметь навыков определения типов отказов и их причин. Для этого могут потребоваться компетенции инженера по надежности или инженера по техническому обслуживанию.
После тщательного анализа вы обнаружите, что большинство отказов происходят на небольшом количестве оборудования. Вопрос заключается в том, какое это оборудование?
Шаг 2. Анализ критичности активов
Многие руководители говорят, что они определили свое критическое оборудование. Но в большинстве случаев категория критичности оборудования может изменяться в зависимости от того, на сколько люди расстроены из-за отказов оборудования.
Проблема заключается в том, что люди часто не понимают, какие последствия возникнут вследствие отказа, и какова вероятность наступления этих последствий в случае неэффективного управления надежностью оборудования.
Цель анализа критичности — идентификация оборудования, отказ которого будет иметь наиболее серьезные последствия для целей бизнеса. К таким последствиям можно отнести:
Снижение производственной мощности и (или) загрузки оборудования
Высокая стоимость потерь (включающие как стоимость восстановительных работ, так и потери от простоя оборудования)
Экологические последствия
Вопросы безопасности
И т.п.
Рисунок 6
Результирующее число критичности оборудования используется для приоритизации распределения ресурсов технического обслуживания. Модель этого процесса представлена на Рисунке 6.
По оси «У» перечислены значения критичности активов (от «Нет» до «Высокой». Количество градаций критичности может быть любым, например, можно использовать шкалу 0-1000, потому что все активы не обязательно равны.
По оси «Х» отложена тяжесть последствий, которые могут возникнуть с наступлением того или иного вида отказа каждого из критичных активов.
Таким образом, инженер по планированию, используя точки пересечения линий критичности и тяжести последствий, может выстроить оптимальную последовательность выполнения работ, чтобы уменьшить риски.
Для определения приоритетности работ при составления графика можно добавить еще два фактора. На Рисунке 7 приведена четырехфакторная модель приоритизации работ, где помимо критичности активов и тяжести последствий, учитывается тип задания на работы (профилактика, ремонт, проверка и т.д.) и время ожидания, которое эта работа находится в списке к выполнению.
Необходимо определить, какое оборудование вероятнее всего может повлиять на эффективность производства. Именно это оборудование в первую очередь должно быть включено в программу повышения надежности.
Последовательное ранжирование критичности активов позволяет обеспечить выполнение нужных работ в нужное время, что является ключевым фактором в предупреждении и устранении отказов оборудования.
Шаг 3. Анализ отказов
Цель большинства стратегий технического обслуживания заключается в прогнозировании и предупреждении отказов оборудования.
Отказ оборудования, как правило, вызван катастрофическим отказом его отдельного узла. Отказы узлов происходят в случае развития дефектов, против которых не принимается никаких мер. Эти дефекты, в свою очередь, вызваны чем-то, то есть имеют свои причины. Таким образом, устранение причины дефекта отдельного узла предотвратит отказ всего оборудования.
Основная задача профилактического технического обслуживания — устранение причин и предотвращение отказов оборудования.
Основная задача предиктивного (прогнозного) технического обслуживания или технического обслуживания по состоянию — обнаружение дефектов и управление потенциальными отказами прежде, чем они станут функциональным отказом.
Многие компании реализуют программы, основанные на стратегии профилактического (предупредительного) технического обслуживания, но ни одна из них, как правило, не учитывает специфику разных видов отказов.
Например:
Роликовые подшипники в электродвигателе имеют определенные режимы отказов, которые могут быть предотвращены при соблюдении режима смазывания.
Дефект «Износ» возникает в подшипнике по причине «Недостаток смазывания».
Возникает вопрос, в чем причина отсутствия нужного количества смазки в подшипнике?
Недостаточный уровень смазки может быть обнаружен по причине отсутствия утвержденной карты смазывания подшипников. Другими словами, обслуживающий персонал может произвести смазывание, но, не зная требуемого количества смазки, не может защитить подшипник от износа.
Лучший путь для обнаружения разных типов отказов — это облегчение процесса идентификации отказов. Соберите небольшую команду опытных людей, обучите их концепции «Деталь» — «Дефект» — «Причина» и пройдите с ними по всему основному оборудованию на предприятии, такому как центробежные насосы, поршневые насосы, редукторы, двигатели и т.д. Вы увидите, что относительно небольшое количество кодов отказов будет покрывать большую часть видов отказов на вашем заводе. Описанные во время этого упражнения виды отказов будут в дальнейшем использованы при проведении RCA, RCM и в других методиках.
Если в течение одного года доминирующим видом отказов подшипников будет являться «Износ», вызванный недостаточным смазыванием, то вам надлежит разработать стандарт смазывания или пересмотреть существующий документ, а также провести обучение персонала. Таким образом вы устраните большое количество отказов на всем вашем оборудовании.
Проблема в том, что большинство компаний ничего этого не делают. У вас нет данных, чтобы выявить единую, главную проблему для нескольких активов (нет унификации данных об отказах, которые можно использовать при формировании отчетов).
Пример:
Не мотор отказал, а мотор отказал по причине вида отказа конкретной детали, в результате отказа которой произойдет разрушение мотора. Если конечно дефект данной детали не будет выявлен на достаточно ранней стадии вида отказа.
Шаг 4. Стратегия технического обслуживания
Стратегия обслуживания должна являться результатом мероприятий по проведению анализа видов, причин и последствий отказов, RCM-анализа, собранных данных об отказах из вашей CMMS / EAM.
«Стратегия уничтожения: Наилучший путь устранить смертельные потери — это лучше понять настоящую природу паттернов отказов оборудования и настроить в соответствии с ними стратегию обслуживания».
Andy Page, CMRP
Что же такое стратегия обслуживания? Давайте разобьём это понятие на два слова.
Обслуживание — это поддержка состояния, защита функций, сохранение требуемой производительности оборудования.
Стратегия — это разработка конечного плана для достижения поставленной цели.
Таким образом, стратегия технического обслуживания определяет те мероприятия, которые вы должны запланировать и провести для поддержки, сохранения и/или защиты ваших активов.
Имейте в виду, существует стратегия технического обслуживания «Работа до отказа» («Run to failure», RTF), однако она применима только в том случае, когда анализ определил ее как лучшее решения для оптимизации надежности по оптимальной стоимости для конкретного оборудования.
Техническое обслуживание с меньшим вмешательством в работу оборудования предпочтительней, чем более инвазивное обслуживание. Это одна из фундаментальных концепций любой четко определенной стратегии обслуживания. Конкретные стратегии обслуживания предназначены для уменьшения последствий каждого вида отказа. В результате — техническое обслуживание концентрируется на обеспечении надежности функции оборудования, а не на выполнении ремонта оборудования. То есть можно сказать, что прогнозное (предиктивное) техническое обслуживания или мониторинг состояния — это лучшее решение, поскольку в этом случае минимизируется вмешательство в работу оборудования.
Стратегия технического обслуживания, которая ориентирована только на обнаружение и предотвращение дефектов, никогда не сможет предотвратить системные и оперативные проблемы активов. Механики всегда будут слишком заняты устранением симптомов отказов вместо того, чтобы устранять их причины. Для того, чтобы обслуживание действительно было проактивным, необходимо научиться идентифицировать и устранять первопричины дефектов оборудования. Стратегии, которые способны решать эти задачи — приводят к поэтапному повышению производительности и позволяют достигать невероятной экономии средств. Стратегии, которые не пытаются решить проблему устранения первопричин отказов — всегда будут иметь слабые результаты, в том числе и по экономической эффективности. Стратегия обслуживания должна включать в себя все элементы, которые фокусируют план технического обслуживания на достижение цели бизнеса.
Прогнозное и профилактическое техническое обслуживание — ключевые элементы стратегии сервиса.
Планирование технического обслуживания, ориентированное на устранение причин отказов, состоит из повторяющихся процедур на основе запланированных работ на критичном оборудовании строго по графику, выполняемых по методике точного технического обслуживания, с соблюдением правил ввода в эксплуатацию после замены запасных частей или ремонта оборудования и контролем качества выполнения работ с помощью функции «Прогнозирование», для предотвращения дефектов, которые могут возникнуть после обслуживания. Финальной частью стратегии технического обслуживания является PRACAS, поскольку он способствует непрерывному совершенствованию этой стратегии.
***
Отчеты об отказах
Форма отчета об отказах может быть любой. Главное, необходимо установить и дисциплинированно выполнять регламент анализа отчета об отказах за определенный период времени и разработать мероприятия по устранению причин выявленных дефектов.
Ниже приведены некоторые примеры отчётов которые следует включить как часть вашего FRACAS.
1. Состояние активов или процент активов без идентифицируемых дефектов
Рисунок 8
Отчет о состоянии активов или процент активов с неидентифицированными дефектами готовит служба технического обслуживания для руководства предприятия, по крайней мере, ежемесячно (см. Рисунок 8).
Про активы, которые имеют идентифицированные дефекты говорят, что они находятся в красной зоне, активы, не имеющие идентифицированных дефектов — в зеленой зоне. Вот и все. Все очень просто. Нет никаких других «но если», «что если» или «если затем». Если существует идентифицируемый дефект актива, то актив в красной зоне, если нет опознаваемых дефектов — в зеленой.
Процент оборудования, которое находится в зеленой зоне, является показателем Здоровья Активов.
Дефект — это аномалия в детали оборудования, которая, может привести к отказу актива, если своевременно ее не устранить.
Пример:
Завод имеет 1000 единиц оборудования.
Из этого числа 750 единиц не имеют идентифицируемых дефектов.
Сообщается, что завод имеет 75%-е здоровье активов.
Есть интересный аспект, касающийся здоровья активов. Здоровье активов стало опережающим ключевым показателем эффективности затрат на техническое обслуживание и бизнес-рисков, то есть тем показателем, который очень информативен для менеджмента сервиса и производства.
2. Среднее время между отказами и среднее время ремонтов
Этот отчет инженеры по надежности ежемесячно готовят на 5-20% критичного оборудования. Отчет делается с целью улучшения обоих показателей. Сами показатели должны быть измерены и представлены для сравнения на линейной диаграмме.
3. Расхождение затрат между участками завода.
Отчет о стоимости технического обслуживания готовят специалисты по своим зонам ответственности и предоставляют руководству по техническому обслуживанию и производству на ежемесячной основе. Отчет не может быть принят, если он не содержит описания причин расхождения и плана приведения расходов в соответствие.
4. Наиболее частые «Деталь»-«Дефект»-«Причины»
Этот отчет ежемесячно готовят инженеры по надежности. Если у вас нет специалистов по техническому обслуживанию или инженеров по надежности, то вам следует выбрать пару наиболее опытных в вопросах надежности механиков и поручить им выполнять функции инженеров по надежности. Для этого необходимо обучить их основным принципам идентификации, предупреждения и устранения отказов.
Этот отчет позволит вам выявить основные потоки отказов и принять меры для их устранения.